The 2nd Coentunnel
The 2nd Coentunnel has to solve the traffic congestion around Amsterdam. The project consists of construction of an immersed tunnel under the North Sea Canal. The closed part of the tunnel consists of four immersed tunnel elements (30 meter wide and 660 meter long in total) and two service buildings. Together with the open approaches, the tunnel is 1064 m long.
The new tunnel has been immersed at a close distance to the existing Coentunnel. To ensure stability of the existing tunnel while dredging a trench next to it a steel sheet pile wall, with piles of 1500mm in diameter, was constructed between the existing tunnel and where the new tunnel would be constructed. In order to manage the risks involved, specific precaution measures have been taken to protect the existing tunnel. The tunnel structure has been prepared to take the loading of a sunken ship and the impact of a dropped anchor.
The elements of the tunnel were built in the Barendrecht casting yard and had to be transported over sea for over 150 km. To withstand the waves the elements were prestressed before transport, these presstress were cut to allow the tunnel section to settle on the river bed.and behave like the shackles of a chain. This concept of a flexible tunnel reduces the forces in the tunnel which could arise when uneven settlements occur or backfill loads are imposed on the tunnel
The new tunnel has been immersed at a close distance to the existing Coentunnel. To ensure stability of the existing tunnel while dredging a trench next to it a steel sheet pile wall, with piles of 1500mm in diameter, was constructed between the existing tunnel and where the new tunnel would be constructed. In order to manage the risks involved, specific precaution measures have been taken to protect the existing tunnel. The tunnel structure has been prepared to take the loading of a sunken ship and the impact of a dropped anchor.
The elements of the tunnel were built in the Barendrecht casting yard and had to be transported over sea for over 150 km. To withstand the waves the elements were prestressed before transport, these presstress were cut to allow the tunnel section to settle on the river bed.and behave like the shackles of a chain. This concept of a flexible tunnel reduces the forces in the tunnel which could arise when uneven settlements occur or backfill loads are imposed on the tunnel
Amsterdam,
Netherlands
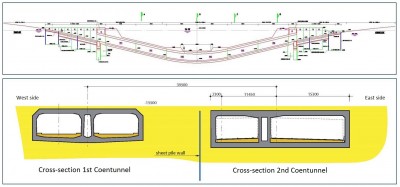
Rijkswaterstaat
Coentunnel company
165 meter
660 meter
-24.4 meter
€500 million
Project construction
2009-05-01
2013-05-13
2013-05-13
4 Elements
5 Lanes
8.4 meter
30 meter
Close (19 meters) to the already existing 1st Coentunnel.
Traditional formwork was used. First the floor slab was cast, then the central gallery. Finally the outer walls and roof slab were cast. Cooling was used to prevent early age cracking due to hydration heat gradients and imposed deformations.
The tunnel elements were immersed using a sheerleg, they were placed on a temporary foundation using hydraulic rams, after which the gap below the tunnel element was filled with a water-sand slurry. After complete filling of the gap the hydraulic rams wer
The primary waterproofing in the immersions joints was provided by Gina gaskets. Secondary waterproofing was provided by Omega-seals which were bolted to cast-in steel I-beams.
The foundation of the elements consist of 500 prefab piles and 1500 vibro-combination piles. The longest piles are up to 40m beneath the ground level.